The importance of battery management is self-evident. More and more products are moving in the direction of portability, enabling users to achieve unprecedented independence. A few decades ago, cordless phones were the first to offer people the freedom to walk at home. Nowadays, portable rechargeable products enable people to stay in touch with their families while traveling around the world. More and more products use rechargeable batteries, and as the size of the product shrinks, the complexity of these products continues to increase. The rechargeable battery itself is also changing, and battery manufacturers are working hard to introduce new products that adapt to the rapidly changing market. The battery voltage is increasing, the form factor is changing, and the energy density is climbing. Consumers continue to understand the battery, they need more flexibility, longer working hours, lower cost and higher security. Microchip has been working on simplifying system design with PIC microcontrollers for many years. Microchip is currently applying this technology to the battery management product line to simplify and better manage the charging system.
This article refers to the address: http://
method
First, divide a typical battery management system into four modules: charging, protection, fuel gauge, and safety:
Charging
A secondary battery-based battery pack is different from a primary battery pack, and the secondary battery pack needs to be charged after use, instead of being discarded like a primary battery. The variety of charging circuits and charging algorithms are diverse, and they are properly charged for a particular chemical type of battery in its unique system environment. The location of the charger should also be properly selected. Whether the charger is a stand-alone unit: whether it is a charger or a direct charge through the converter; whether the charger is integrated in the system or in the battery pack; other important considerations include charging time, temperature range and noise requirements. Microchip offers a wide range of charge management products for linear chargers in single or dual cell Li-Ion/Polymer battery packs. Linear chargers have low output noise and are important for systems that send and receive voice and data.
For designs that require high efficiency and low power consumption, the PS200 switch mode charge controller has a maximum switching frequency of 1 MHz. It contains algorithms for charging lithium, nickel and lead acid batteries. Due to the complexity of the design of the switching charger, Microchip offers software tools to guide designers through the configuration of the IC and the generation of the circuit diagram. Another solution for the standard industry offering charger products is to use a fuel gauge IC with a charge controller. The PS501 has a pulsed charging circuit to control general purpose inputs/outputs to meet this requirement. This topology provides a very compact and cost effective solution. The charging portion of the system is separated, and Microchip has the algorithms it needs to optimize charging, including maximizing charging, reducing charging time, and maximizing customer satisfaction.
2. Protection
When using lithium ion/polymer batteries, protection must be provided because overcharging or overheating can cause fire or explosion. Lead-acid or nickel batteries do not require protection, but they are often protected against damage or degradation. The primary protection circuit is a dedicated circuit that detects if an unsafe condition has occurred and shuts down the battery pack to prevent damage when an unsafe condition is detected. The secondary protection circuit prevents the battery from continuing to charge and/or discharge under unsafe conditions. In the event of a failure of the primary protection circuit, the resettable secondary circuit provides backup protection. Users can also add additional levels of protection, such as chemical fuses, which can permanently turn off the battery pack when other levels of protection fail. Dedicated safety ICs are typically used for primary protection circuits. Battery management ICs are ideal for secondary protection and stable protection circuits because they do not add additional cost to the solution. Micorchip's fuel gauges, such as the PS501 and PS810, monitor the voltage, battery pack voltage, current and temperature of each cell. The general purpose input/output (GPIO) pins have powerful configuration features to set and reset any possible fuel gauge conditions. This flexibility allows the fuel gauge to meet very complex safety requirements.
3. Electricity metering
Electricity metering is not just monitoring the current flowing into and out of the battery pack. Accurate fuel metering requires a systematic approach that takes into account typical usage patterns, environments, and customer expectations. Ideally, battery management ICs provide users with good performance while providing the system with the information they need to make intelligent choices to improve system performance. Intelligent fuel gauge algorithms extend system uptime and battery life and provide additional security by accurately detecting full charge and full charge points. They also detect and avoid battery imbalances and overheating. These algorithms can be adjusted based on system conditions and can slow down battery aging. They use a configurable model of battery behavior to ensure that the losses caused by self-discharge and charging are correctly calculated. These algorithms can be customized by the customer so that the user only accepts relevant information without having to worry about an unexpected shutdown that can result in data loss. Microchip's fuel gauge products are enhanced to make fuel gauges more reliable.
Unexpected system shutdown is one of the most unpleasant things when using portable devices, and most people should feel the same. It will reduce customer satisfaction, and it will cause significant data loss and significant loss of time and money. Unexpected shutdown typically occurs when the battery voltage drops below the level required by the support system. When the load increases, the battery voltage is greatly reduced, especially when the discharge line will end, at which point the slope of the discharge curve increases. To avoid accidental shutdowns, Microchip uses an algorithm based on energy demand information when the system is shut down, as shown in the following figure. The fuel gauge automatically selects the appropriate shutdown point to ensure that there is enough residual energy to alert the user and save the data. The shutdown point will also change over time. As the battery ages, the full charge capacity decreases and the voltage of the discharge curve changes. The aging algorithm adjusts the shutdown point to ensure that energy is not wasted as the battery ages.
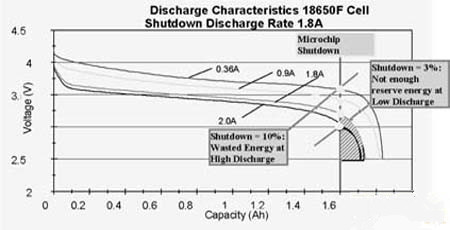
4. Security
Systems with removable battery packs should be secured to prevent the system from operating under unreasonably designed battery drives. If the system uses an unsteady chemical battery, overcharging or overdischarging may result in an unsafe condition. If a steady-state chemical battery is not used in accordance with the manufacturer's requirements, it may result in reduced performance and reduced life. Simple mechanical barriers are used today, such as the use of unique form factors or connectors, as well as the read position from the battery. But unfortunately, these security measures are easily broken. What users really need is a flexible, system-level solution that ensures user safety, improves system performance, and provides long-term reliability.
Microchip offers a good solution for battery verification, the KEELOQ° encryption algorithm, which provides industry-proven security for a wide range of applications. KEELOQ algorithms are required for both host and peripheral applications. Hardware. Today, the KEELOQ algorithm has been applied to a variety of security systems, such as keyless entry systems (primarily used in the automotive industry). When using KEELOQ technology for battery verification, the system is the host and the battery is the peripheral. The system stores the manufacturer code and a random number generator. When the battery is made, a unique serial number and key are generated and stored in memory and will not be changed. When the battery is connected to the system, the system will request a serial number and send a 32-bit challenge. The battery will provide the corresponding serial number and give a 32-bit response. Due to the wide variety of battery management systems, Microchip uses KEELOQ technology in its battery management products and many PIC microcontroller products. When using Microchip's fuel gauge in a battery pack, the system is safe without additional hardware. If there is no fuel gauge in the battery pack, you can use the PIC microcontroller as the KEELOQ peripheral hardware. Host hardware that supports KEELOQ technology includes processors, fuel gauges, and chargers.
The module diagram is as follows:
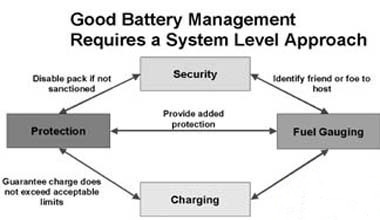
Planning and partitioning
When designing an application that uses a secondary battery as a power source, planning the charging system at the product design stage is critical. This problem is often taken seriously in the later stages of system development, resulting in poor system performance, because many compromises must be made at this time. Partitioning is important because the location of each module in the charging system tends to affect the choice of ICs and circuits, and how these modules interact. The initial plan includes a list of system requirements for battery power. When choosing the battery chemistry type, the actual size, weight requirements, run time and storage temperature range are all important. Table 2 summarizes the most common chemical batteries.
Factors that determine battery pack configuration are: minimum/maximum and nominal voltage values, charging current, discharge current, and charging capacity required to meet operational requirements. Most systems require charging, but there are a few special systems exceptions. Whether the charger is placed in the system, in the battery pack, or outside the system is also an important consideration. An embedded battery can place the charger in the system, but it is inconvenient for a removable battery pack, especially if the user has multiple battery packs. Some devices have both a built-in charger and an optional external charger. The built-in charger in the battery pack allows the battery pack to be recharged both inside and outside the system. The battery and system requirements determine the topology of the charger. Table 3 shows a comparison of the two commonly used chargers in several important ways.
The following discussion discusses whether electricity metering is required. To extend battery life, fuel gauges provide accurate battery information for any operating conditions. It enables dynamic power management and is at the heart of a battery management system with excellent performance. An important factor in this is what communication interface is used between the fuel gauge and the system to exchange information. Two-wire interfaces and single-wire interfaces are available. Of course, if some other part of the system already uses some kind of communication protocol, it is recommended to use the same protocol to communicate with the fuel gauge. If the battery pack is detachable, it is an important factor when the fuel gauge is placed in the system or in the battery pack. If you need to save the historical data and usage information required for the warranty, it is best to place the fuel gauge in the battery pack. For systems with multiple detachable battery packs, the fuel gauge built into the system cannot record this information. Another important consideration is whether the battery information is included in the system display or is displayed separately, or both. Some detachable battery packs contain a small charge status display so you don't have to plug the battery into the system to see how much charge is left. Finally, if the battery pack has a protective circuit, then a separate safety IC, fuel gauge, or both can be used to perform secondary protection of the battery.
It is very important to follow the battery supplier's recommendations for safe operation. If the battery has a verification function, the system reacts to an unrecognized battery. Portions of the system, such as the charging section, can be turned off and the entire system can be powered down. There are many options for the design of the battery management system. Care should be taken to determine which battery management modules are implemented and how the functions of each module are divided in the system. Early planning will help to lay a good foundation for the system.
optimization
For optimal system performance, you should spend some time optimizing your charging operation. It is important to perform in-system testing to identify and correct deficiencies that may degrade system performance and user experience. In-system testing includes ensuring that the system meets performance requirements at the expected temperature and discharge rates; determining which information is needed by the user and displaying it in a comprehensive and understandable manner.
to sum up
The power provided by the battery brings vitality to the system. Good battery management should be “seamless†for the user, and it is the basis for a delightful product experience. Poor battery management will make the product a success. As an integral part of the system, battery management should be well understood and planned and optimized in advance. With Microchip's battery management devices and algorithms, all battery management functions can be implemented in different topologies. Linear and switching chargers can be used to charge outside the battery pack. The linear charger only supports lithium batteries, while the switch mode charge controller contains algorithms for charging lithium-ion, nickel, and lead-acid batteries. The built-in charge control of the battery pack can be achieved using the fuel gauge IC. Microchip's fuel gauge ICs include a variety of algorithms for accurate fuel gauge, charge control, and redundancy protection for nickel or lithium batteries. With a well-planned, well-designed, and Microchip's battery management expertise, the ideal battery management system will lay the foundation for product success.
Ningbo Xingchuangzhi Electric Appliance Co.,Ltd. , https://www.xingchuangzhi.com